Before You Specify Thermally Modified Wood, Read This
Thermally modified wood has quickly gained traction in architectural circles as a forward-thinking alternative to pressure-treated lumber and tropical hardwoods. Its promise of improved dimensional stability, enhanced decay resistance, and reduced chemical usage has made it an attractive option for exterior applications like decking, cladding, and siding.
At first glance, it seems like a win: take a common wood species, apply heat in a controlled environment, and create a more durable material with a refined aesthetic. But like many emerging building products, the story of thermally modified wood is more complex than its marketing suggests.
This article takes a closer look at what’s actually happening during the thermal modification process — how it alters the wood’s cellular structure, how those changes impact real-world performance, and what architects should be aware of when specifying this material. Through a careful examination of the science, we’ll unpack some of the lesser-known realities behind thermally modified wood — and the trade-offs that often go unnoticed.
If you're looking to design with longevity, resilience, and sustainability in mind, these are details worth knowing.
What Is Thermally Modified Wood?
Thermally modified wood refers to lumber that has been altered through a high-heat treatment process in the absence of oxygen. The goal is to change the physical and chemical properties of the wood to make it more dimensionally stable and less susceptible to rot, fungi, and insects.
The Process: How It Works
The thermal modification process involves heating the wood in a kiln or chamber to temperatures typically between 160°C and 220°C (320°F to 428°F). Oxygen is reduced or eliminated during this process to prevent combustion. The high heat drives moisture and volatile organic compounds (VOCs) out of the wood and breaks down hemicellulose — one of the key components in cell wall structure that fungi feed on.
This treatment reduces the wood’s ability to absorb water, which can help minimize swelling, shrinking, and warping in changing climates. At the same time, the breakdown of organic matter makes the wood less attractive to pests and more resistant to decay.
Species Commonly Used
Because the process is designed to improve lower-grade species, most thermally modified products start with softwoods or temperate hardwoods like:
- Ash
- Poplar
- Spruce
- Pine
- Beech
- Birch
These species are generally abundant, fast-growing, and inexpensive — but also lacking the natural durability needed for long-term exterior use without chemical treatment or modification.
By modifying these woods, manufacturers can offer a material that performs better than its original form, while maintaining a sleek, uniform appearance.
The Science Behind the Modification: What’s Really Happening?
Thermal modification changes wood at a molecular level. The process removes moisture, volatile organic compounds, and hemicellulose — one of the sugars fungi rely on to colonize wood. As a result, the wood becomes less biologically active, which enhances its resistance to decay.
But while some benefits are gained, they come with a set of less-publicized trade-offs that directly affect the material’s long-term performance.
Brittleness and Structural Integrity
One of the most important — and often overlooked — consequences of thermal modification is increased brittleness. As the wood is heated to extreme temperatures, its cellular structure begins to degrade. Hemicellulose and other binding compounds break down, making the wood more brittle and prone to cracking or splitting under stress.
This can limit how and where thermally modified wood is used, especially in applications that involve:
- Fasteners or screws (which can cause splitting)
- Load-bearing or high-traffic surfaces (like decking)
- Curved or shaped designs (where flexibility is needed)
Even though the wood is more dimensionally stable post-treatment, it’s also mechanically weaker. Over time, this brittleness can lead to surface checking, splintering, and reduced load capacity — particularly in climates with seasonal movement.
Aging and Strength Loss Over Time
Thermally modified wood isn’t just brittle when new — it also tends to weaken further as it ages. The loss of natural elasticity and the breakdown of structural carbohydrates make it less resilient over the years. In exterior applications exposed to sun, wind, moisture, and freeze-thaw cycles, this aging process can accelerate, undermining the lifespan that was promised at installation.
Energy Demands and Carbon Footprint
While often marketed as a sustainable alternative to chemically treated wood, thermal modification comes at a high environmental cost. The heat treatment process requires significant energy — often in the form of fossil fuels — to sustain kiln temperatures for hours or even days. In many cases, this energy input outweighs the benefits gained from avoiding chemical preservatives.
Furthermore, thermally modified wood is often imported from overseas. Many of the popular species used in thermal modification — like ash or spruce — are sourced and processed in Europe, then shipped to North America for resale. This long supply chain increases the carbon footprint dramatically compared to domestically available, naturally durable alternatives.
Real-World Performance: The Trade-Offs in Durability
On paper, thermally modified wood appears to offer durability improvements over untreated softwoods. In controlled environments, it resists fungal decay and demonstrates good dimensional stability. But in the field — where conditions are rarely controlled — the long-term performance tells a more nuanced story.
The Strength-Durability Dilemma
Thermally modified wood may resist rot, but it does so by sacrificing strength. Unlike naturally durable hardwoods that combine decay resistance and structural integrity, thermally modified woods trade mechanical performance for biological stability. This trade-off becomes especially noticeable in demanding applications like:
- Decking under frequent foot traffic
- Outdoor stairs and platforms
- Furniture and structural joinery
- Installations requiring fastening or mechanical fixing
In these settings, the loss of elasticity and toughness can result in cracked boards, broken edges, or screw-split fastener holes — issues that are rarely evident in lab reports, but frequently observed by contractors and clients over time.
In fact, a field study conducted by the U.S. Forest Service found that thermally modified wood, while initially resistant to decay in lab tests, showed inconsistent durability when exposed to real-world outdoor conditions. Boards placed in severe weathering sites deteriorated faster than expected — underscoring the gap between promotional claims and on-site performance. For architects, this highlights the importance of specifying materials with a proven track record, not just controlled-environment data.
Surface Checking and Splintering
Due to the brittleness introduced during thermal modification, the wood is more prone to surface checking (fine cracks) and splintering, particularly in areas exposed to sunlight and moisture cycles. This not only affects the aesthetic longevity but can also become a safety concern in barefoot traffic zones like residential decks, rooftop terraces, and outdoor walkways.
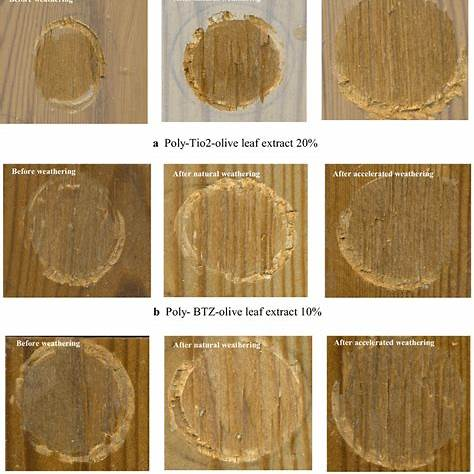
Lifespan Variability
While some manufacturers claim lifespans of 20–30 years for thermally modified wood, these estimates can vary widely depending on species, treatment method, installation conditions, and maintenance. In many cases, accelerated weathering and mechanical failures begin to appear well before those benchmarks — especially if the wood was improperly fastened or left untreated.
Unlike naturally rot-resistant woods, thermally modified products do not continue to harden or improve with age. Their lifespan is more linear: the moment they leave the kiln, the clock starts ticking.
Weathering, Color Fading, and Aesthetic Challenges
One of the main draws of thermally modified wood is its rich, darkened tone — a result of the high-heat process that caramelizes the wood's natural sugars. The result is a uniform, toasted appearance that mimics the look of tropical hardwoods like Ipe or Teak. In marketing photos and freshly installed projects, this aesthetic is striking. But the reality over time tells a different story.
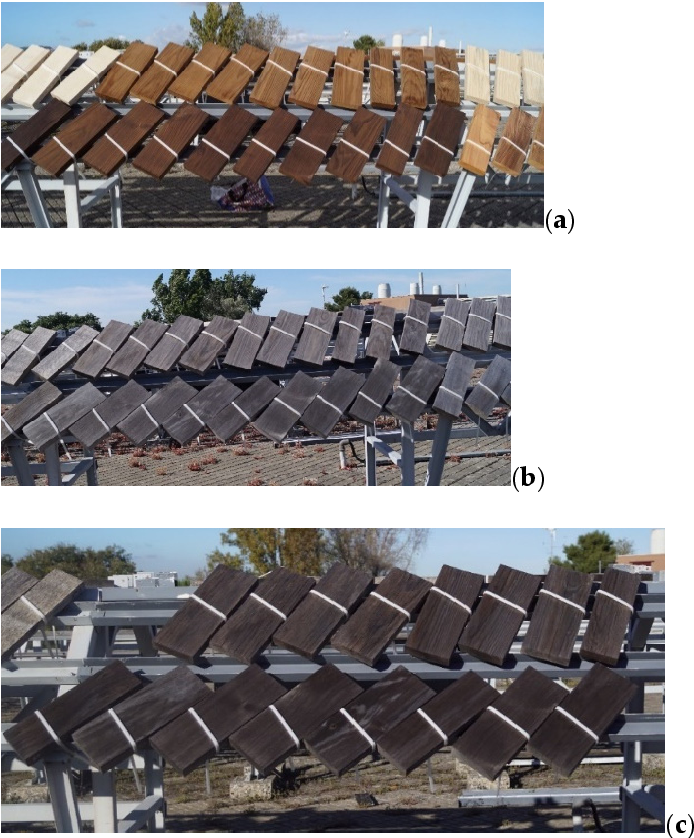
UV Exposure and Uneven Fading
Like all wood, thermally modified boards are susceptible to ultraviolet (UV) degradation. Without consistent treatment or sealing, the original dark tone quickly fades to a muted gray — often unevenly. This uneven patina can be particularly noticeable on decks, where foot traffic, shade, and water exposure vary board to board. The result? A patchy, inconsistent look that requires regular maintenance to correct.
This is especially important for architects specifying outdoor materials for high-visibility spaces like:
- Rooftop decks
- Courtyards
- Outdoor seating areas
- Cladding on residential or commercial facades
Inconsistent fading not only impacts the visual harmony of a project — it can lead to client complaints and unexpected maintenance costs.
Surface Texture and Grain Quality
Thermal modification tends to darken wood uniformly, which can flatten the natural visual depth of the grain. This is particularly true with softwood species like pine or spruce, where the treatment can make boards appear “flat” or dull after a few seasons.
Additionally, the heat treatment can accentuate existing knots, surface checks, and imperfections. These features may not be visible at first, but as the wood weathers, they emerge more strongly and can compromise the refined aesthetic that clients and designers often expect.
Finishing Requirements and Maintenance
To maintain its color and clarity, thermally modified wood requires regular applications of UV-blocking sealants or oils — sometimes annually, depending on climate and exposure. While this is not unique to thermally modified wood, the original appeal of its rich tone creates an expectation that it will last longer than it realistically does without intervention.
In projects where long-term color retention and low maintenance are priorities, these requirements can become an issue — particularly when expectations were set by sales literature, not field experience.
Environmental Considerations: Greenwashing or Green Building?
Thermally modified wood is often presented as the eco-conscious choice — a “natural” alternative to pressure-treated lumber, free of chemical preservatives and marketed as a sustainable material. But when you take a closer look at how it’s made and where it comes from, the green narrative begins to unravel.
Energy-Intensive Process
The very process that gives thermally modified wood its durability is also its most significant environmental liability. Reaching temperatures between 320°F and 430°F for extended periods — sometimes 24 to 72 hours — requires massive energy input. These kilns don’t run on solar panels. In most cases, they rely on natural gas or other fossil fuels to generate and maintain the high heat necessary for modification.
This carbon-intensive process is often overlooked in sustainability discussions. While the final product may be “chemically free,” it comes with a sizable hidden cost in terms of energy consumption and carbon emissions. For projects aiming to meet LEED standards or carbon reduction goals, this is a critical factor to consider.
A peer-reviewed Life Cycle Assessment published in Coatings found that thermally modified wood façades, despite their low emissions during the use phase, had significantly higher environmental impacts during production — mainly due to the energy required to heat the wood and maintain treatment conditions. These embodied carbon levels challenge the assumption that thermal modification is a low-impact process and call for a more nuanced sustainability comparison.
Long-Distance Sourcing and Transportation
Another sustainability blind spot: sourcing. Much of the thermally modified wood sold in North America is not manufactured locally. It’s imported — primarily from Europe, where species like ash, spruce, and pine are grown, harvested, modified, and then shipped across the Atlantic.
This transcontinental journey adds significant embodied carbon to every board. Between extraction, modification, packaging, ocean freight, and distribution, the environmental impact compounds quickly — often surpassing that of locally sourced, naturally durable hardwoods.
Shorter Lifespan = More Waste
While thermal modification increases resistance to rot, it does not extend the wood’s lifespan to match that of denser, naturally rot-resistant species. In fact, many thermally modified products begin to degrade within 15–25 years — sometimes sooner in high-exposure environments.
This shorter service life means more frequent replacement cycles and, ultimately, more material going to landfills. That may not be reflected in the marketing copy, but it’s written all over long-term project performance.
The Case for Stronger, Smarter Alternatives
At a certain point, the pattern becomes hard to ignore. A material that’s engineered to be stable ends up brittle. A process marketed as sustainable turns out to be energy-intensive and carbon-heavy. A product promoted for its longevity quietly shows signs of failure within a decade or two.
Thermally modified wood solves one problem by creating several new ones — and architects are starting to take notice.
In a market filled with marketing claims and engineered fixes, there's growing demand for materials that simply work. No excessive processing. No complicated maintenance schedules. No hidden trade-offs buried in fine print. Just strength, longevity, and natural durability — as expected.
When you’re specifying materials for structures meant to last 30, 50, even 100 years, short-term performance isn’t enough. You need reliability. You need consistency. And you need to be confident that what you're designing today will still deliver for your clients tomorrow.
It’s no surprise that more and more architects are moving away from thermally modified products in favor of alternatives that offer:
- True structural strength — not reduced brittleness
- Natural resistance to rot, decay, and insects — not manufactured imitations
- Minimal maintenance — not yearly upkeep just to preserve appearance
- Local sourcing — not transatlantic shipping and high embodied energy
These shifts aren’t just aesthetic. They’re philosophical. They reflect a deeper commitment to performance, accountability, and authenticity in materials — something engineered wood can imitate, but never quite replicate.
The Black Locust Advantage: Built by Nature, Trusted by Architects
Black Locust isn’t just an alternative to thermally modified wood — it’s a fundamentally better material. No artificial processes, no marketing spin, no trade-offs. Just real, natural performance that’s been trusted for generations and is now redefining what sustainable hardwood can be in modern architecture.
Naturally Durable — No Treatment Required
Black Locust is one of the few native hardwoods with Class 1 rot resistance — the highest rating for durability — placing it in the same league as Ipe and Teak. It naturally resists rot, decay, fungi, and insect damage, even in exposed conditions. No thermal modification. No chemicals. No compromise.
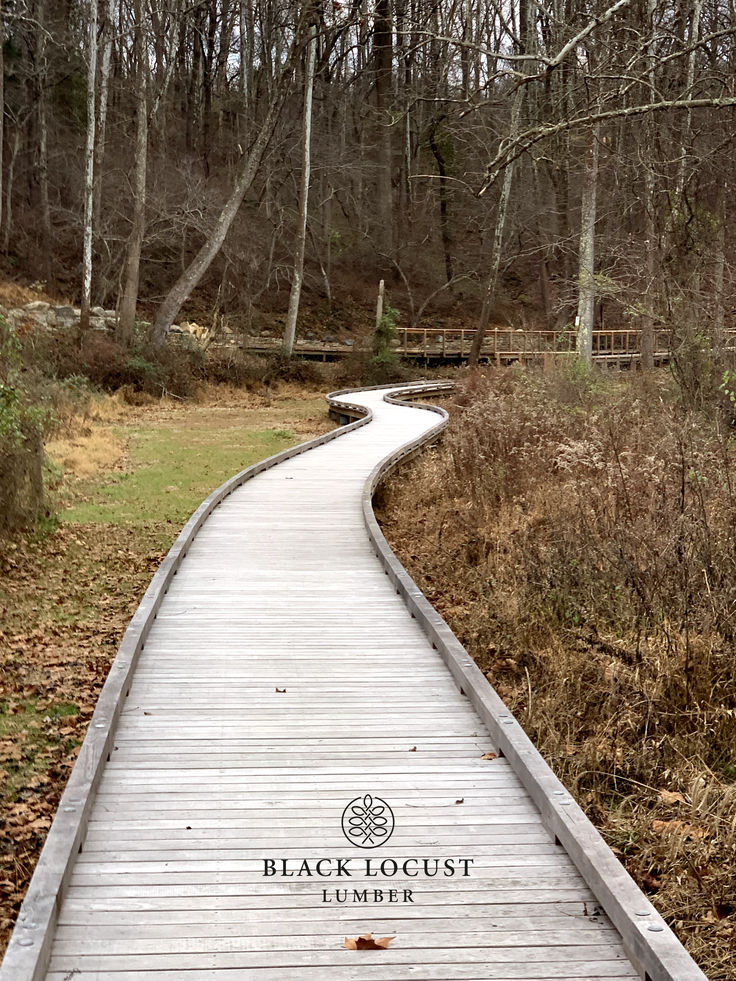
Strength That Lasts Decades
With a Janka hardness rating of over 1,700 lbf, Black Locust is stronger and denser than almost any wood used in thermally modified applications. It handles foot traffic, structural stress, and the elements with ease — making it ideal for decks, walkways, outdoor furniture, and architectural details. And unlike modified products that weaken over time, Black Locust gains stability as it seasons.
Sourced Locally, Designed Responsibly
Black Locust is harvested and milled in the U.S., supporting domestic forestry and reducing the environmental impact of shipping. Its story is deeply rooted in American land stewardship — from early settlers to today’s climate-conscious designers. You can explore more about its unique legacy in our blog, The Historical Journey of the Black Locust Tree.
Effortless Maintenance, Timeless Beauty
Black Locust doesn’t require sealing, staining, or regular oiling to hold up. It naturally silvers with age, developing a uniform patina without checking or splintering. The result is a hardwood that looks better over time — with virtually no upkeep.
For architects who demand longevity, strength, and true sustainability, Black Locust is the material you’ve been looking for — whether you knew it or not. It performs where engineered wood struggles. It lasts where others fail. And it speaks to a design philosophy that values authenticity, environmental responsibility, and enduring quality.
📩 Have questions or want to request a sample?
Get in touch with our team:
👉 blacklocustlumber.com/contact
📧 Or email us directly at sales@bllpro.com
📄 Download the Black Locust Decking Spec Sheet:
👉 View the PDF